slot gacor
ONIC77 ~Daftar Login Situs Slot Gacor Hari Ini Integritas Terbaik 2024
slot
Couldn't load pickup availability
ONIC77 ~Daftar Login Situs Slot Gacor Hari Ini Integritas Terbaik 2024
Daftar login situs slot gacor hari ini ONIC77 memiliki pilihan game slot online resmi integritas terbaik 2024. Sudah dibuktikan oleh jutaan member setia agen slot gacor hari ini ONIC77, mudah menang dan tidak pernah mengalami rungkat sampai saat ini.
Situs slot gacor hari ini ONIC77 menyediakan berbagai link alternatif untuk memudahkan aksesibilitas para pemain dalam mengakses jika terjadi kendala. Situs slot onic 77 juga menawarkan slot gacor hari ini dalam beragam tema yang bervariasi serta imersif untuk memberikan visual yang inovasi dan nyata seperti Gates of Olympus, Sweet Bonanza, Mahjong Ways, Scopa, Cat Purry dan masih banyak lagi.
Selain itu, situs slot gacor ONIC77 telah berkolaborasi dengan 23 provider ternama di industri judi online, sehingga memberikan sensasi bermain yang luar biasa dan tak tertandingi. Dengan begitu, agen ONIC77 dinobatkan sebagai situs slot gacor andalan para slotter untuk meraih benefit yang diinginkan dengan cara mudah dan cepat.
Informasi Utama Situs Slot Gacor Hari Ini ONIC77 | |
RTP Live | ⚡98.99% |
Deposit Receh | 🔥20.000 IDR |
Metode Deposit | 💸Transfer Bank, E-Wallet, Transfer Pulsa |
Judi Online | 🏆Slot Online, Live Casino Online, Togel, Sportsbook, Tembak Ikan, Sabung Ayam |
Daftar Slot Online Gacor Hari Ini Modal Murah, Pasti Maxwin!
Daya tarik yang menjadi acuan para pemain tetap setia kepada agen slot gacor ONIC77, karena adanya pilihan game slot mudah maxwin. Dengan memilih game slot gacor yang tepat, maka dengan mudah Anda meraup bonus hingga ratusan juta rupiah. Berikut ini adalah daftar slot online gacor hari ini modal murah yang pasti maxwin di ONIC77 :
- Sweet Bonanza (Pragmatic Play), RTP 98%
- Gates of Olympus (Pragmatic Play), RTP 97,30%
- Spaceman (Pragmatic Play), RTP 98%
- Mahjong Ways (PG Soft), RTP 96,50%
- Starlight Princess (Pragmatic Play), RTP 97%
Fitur Rahasia Main Slot Online di Link Slot Gacor ONIC77
Bermain slot online di situs ONIC77 membutuhkan strategi untuk gampang menang dan dapat keuntungan besar dengan peluang lebih besar. Selain strategi, Anda juga perlu mengetahui fitur rahasi main slot online yang bisa digunakan pada link slot gacor ONIC77. Dengan fitur ini, Anda dijamin menang maxwin dalam waktu yg tepat! Berikut ini:
Fitur Free Spin Slot
Free spin adalah putaran gratis yang biasa Anda temukan pada mesin slot di situs ONIC77. Fitur free spin ini akan memberikan Anda peluang kemenangan yang sensasional tanpa perlu memasang betting besar.
Fitur Live RTP Up To Date
Fitur live RTP merupakan nilai Return To Player yang wajib semua member tahu. Di agen slot kami, Anda akan diberikan info RTP terbaik pada tiap game slot gacor yang tersedia secara berkala atau up to date.
Fitur User-Friendly
Fitur user-friendly memudahkan para member mengakses link slot gacor hari ini milik ONIC77 via desktop atau mobile. Dengan adanya fitur ini, tentunya Anda tidak perlu mengalami kendala loading lama yang biasa terjadi pada web abal-abal.
Share
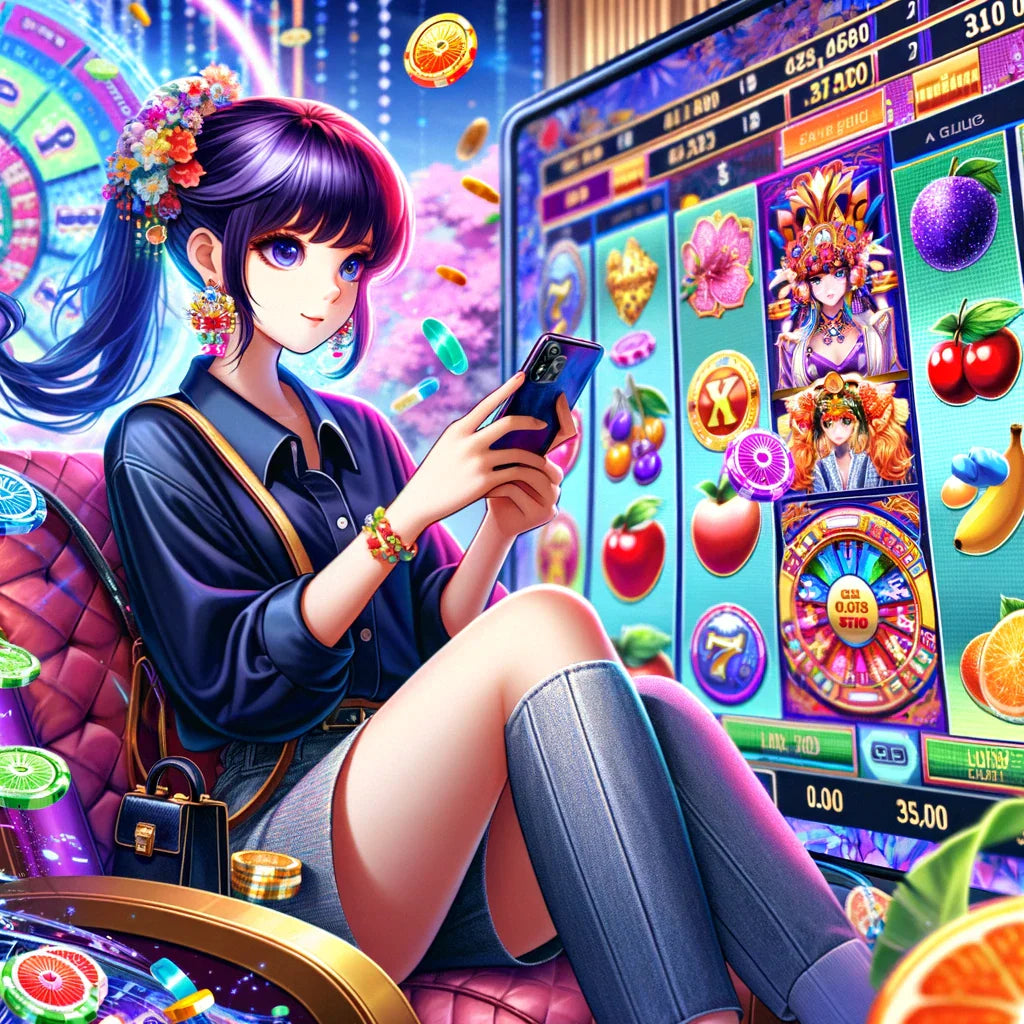
ONIC77 SLOT SITUS TERPOPULER GACOR HARI INI!
ONIC77 ~Daftar Login Situs Slot Gacor Hari Ini Integritas Terbaik 2024
- Choosing a selection results in a full page refresh.
- Opens in a new window.